Treffen Sie uns persönlich oder verfolgen Sie unsere News-Kanäle.
Was uns antreibt
Die optischen Technologien sind Schlüsseltechnologien des 21. Jahrhunderts. So haben sie in Form von Smartphone-Displays oder schnellem Glasfaser-Internet für einen gewaltigen Technologiesprung gesorgt. Herkömmliche optische Systeme wie beispielsweise Projektoren, Mikroskope oder auch Laser bestehen jedoch nach wie vor aus einer Vielzahl an diskreten, optischen Komponenten, welche das zu nutzende Licht erzeugen, manipulieren oder detektieren.
Während eine Mikrointegration im Bereich der Elektronik hin zu elektronischen Halbleiterchips bereits seit Jahrzehnten Standard ist, hat es sich PhoenixD zum Ziel gesetzt, den Erfolg in der Mikroelektronik auf die optischen Technologien zu übertragen. Dafür werden neuartige Prozesstechnologien erforscht und weiterentwickelt, welche die preiswerte und präzise Entwicklung und Produktion integrierter photonischer Baugruppen ermöglichen.
Die Additive Fertigung zählt in diesem Kontext zu den Enablern (dt. Ermöglicher) in der Zielstellung der integrierten Photonik. Wo konventionelle Herstellungsverfahren an ihre Grenzen stoßen, zeigt die generative Fertigung ihre Stärken: Kurze Entwicklungszeiten, integrierte und optimierte Effekte, innovative Gestaltungsmöglichkeiten sowie eine signifikante Reduzierung der benötigten Ressourcen und optimierte Prozessketten.
Durch die Kombination verschiedener Werkstoffgruppen wie beispielsweise Polymere, Keramiken und Glas in einer generativen Prozesskette können maßgeschneiderte Materialeigenschaften und sehr hohe Funktionsintegrationen als Voraussetzung für automatisierte Fertigungen und im Produktlebenszyklus wirtschaftliche Lösungen erreicht werden.
Heute noch sehr aufwendig herzustellende und teure optische Produkte, zum Beispiel aus der Medizintechnik, der Verkehrstechnik oder der Prozesstechnik können so effizienter realisiert und einer viel breiteren Anwendung zur Verfügung gestellt werden. „Wir stellen uns zum Beispiel vor, medizinische Analytik im Taschenformat für jeden erschwinglich zu machen“, sagt Dr. Moritz Hinkelmann, der seit 2020 die Gruppe Optische Systeme in der Abteilung Laserentwicklung am Laser Zentrum Hannover e.V. leitet. Seine Hauptforschungsgebiete umfassen die Simulation und generative Fertigung funktionaler Optiken sowie das Design und die Konstruktion optischer Systeme.
Unsere Forschungsarbeit
Additiv gefertigte Optiken finden aufgrund ihrer Qualität bisher nur in wenigen Bereichen eine Anwendung. An diese Komponenten bestehen hohe Anforderungen in den Bereichen der optischen Qualität und der Eigenschaften des Bauteils. Das gefertigte Bauteil muss folglich unter anderem eine definierte Brechzahl und Transmission (Durchlässigkeit), einen geringen Wärmeausdehnungskoeffizienten und eine ausreichende Homogenität aufweisen. Eine weitere Herausforderung besteht darin, die Fertigung optischer Elemente mit einer geringen Oberflächenrauheit und Materialkombinationen in einen Prozess zu integrieren.
Im Bereich der Additiven Fertigung optischer Komponenten und Systeme haben sich verschiedene laserbasierte Verfahren etabliert, welche unterschiedliche Größenskalen und Präzision adressieren [1]. Dabei wird insbesondere auf transparente Polymere, Silikon [2,3] und Quarzglas zurückgegriffen, um funktionale Optiken zu fertigen. In der Task Group M2 werden diese Ansätze zur Fertigung transparenter Optiken in mehreren Teilprojekten hinsichtlich Prozessoptimierung, Simulation und Qualität der optischen Eigenschaften erforscht.
Im Bereich der optischen Systeme mit diskreten Komponenten wird heutzutage überwiegend auf Quarzglas zurückgegriffen, welches in aufwendigen Prozessen, oft manuell verarbeitet wird. Durch die Additive Fertigung von Quarzglas ergeben sich neue Möglichkeiten hinsichtlich des Designs und somit der Anwendungen.
Der 3D-Druck von Glas ist jedoch ein nahezu unerforschtes Gebiet, welches in einem sogenannten Laser Glas Deposition Prozess weiterentwickelt wird [4]. Hier wird mittels CO2-Laserstrahlung ein Glasfilament additiv auf einem Glassubstrat aufgetragen (Abbildung 1).
Neben klassischen Lichtwellenleitern [5,6] können so auch strukturelle Elemente wie beispielsweise gewichtsarme Versteifungen von Scannerspiegeln gedruckt werden. Die entsprechende Auswahl geeigneter Prozessparameter erfolgt mit Hilfe eines neuen Simulationsmodells, welches den Fertigungsprozess und so die für die Auswahl eines geeigneten Prozessfensters wichtige Temperaturverteilung nachbildet



In einem anderen Projekt wird das Potenzial hochtransparenter Silikonwerkstoffe untersucht. Diese Materialien profitieren von ihrer hohen Beständigkeit gegenüber UV-Strahlung, Temperatur- und Umwelteinflüssen sowie von hoher Materialflexibilität und geringer Dichte. Es werden verschiedene Silikone hinsichtlich ihrer Eignung für optische Anwendungen untersucht (siehe Abbildung 2). Basierend auf den Materialanforderungen werden geeignete Fertigungsverfahren methodisch entwickelt und anschließend umgesetzt.
Hier kommen Freeform-Reversible-Embedding [7] Technologien zum Einsatz, in denen eine Materialkombination selektiv in eine nichtreaktive Flüssigkeit eingeführt wird und durch UV-Strahlung aushärtet. In Zukunft werden so temperaturbeständige, Silikon-basierte Freiform-Optiken kostengünstig und mit niedriger Oberflächenrauheit generativ gefertigt werden und Möglichkeiten entwickelt, diese basierend auf der Flexibilität des Silikons durch Aktoren in ihrer Geometrie und damit in ihren optischen Eigenschaften zu manipulieren.
Neben den oben genannten Verfahren, in denen das Material lokal in die Prozesszone zugeführt wird, können ganze optische Netzwerke über Rolle-zu-Rolle Verfahren oder auf Glas-Wafern in kürzester Zeit kostengünstig gedruckt werden. Dieser Flexographic Printing genannte Ansatz ermöglicht die individualisierte Massenproduktion von planaren Sensornetzwerken [8], welche beispielsweise für hochintegrierte Datennetzwerke eingesetzt werden können und, in Kombination mit im Batch-Prozess gefertigten Elementen, auch für Anwendungen mittlerer Leistungen eingesetzt werden sollen.
Eine Möglichkeit zum Schreiben von vergrabenen, einmodigen Wellenleitern bietet das sogenannte Femtosecond Direct Writing [9]. Hierbei werden Femtosekunden-Laser zum gezielten Strukturieren von Polymeren im Volumen eingesetzt. Durch die hohen Intensitäten im Fokus des Laserstrahls wird ein Plasma erzeugt, welches lokale Materialspannungen und somit eine Änderung des Brechungsindex induziert.
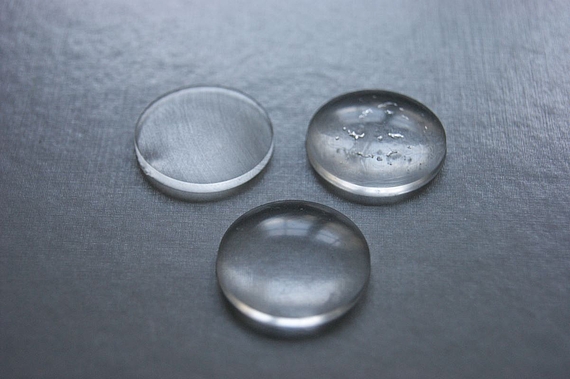
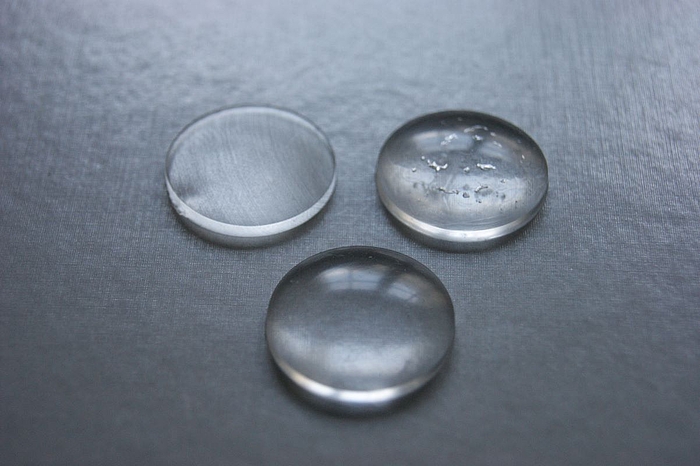
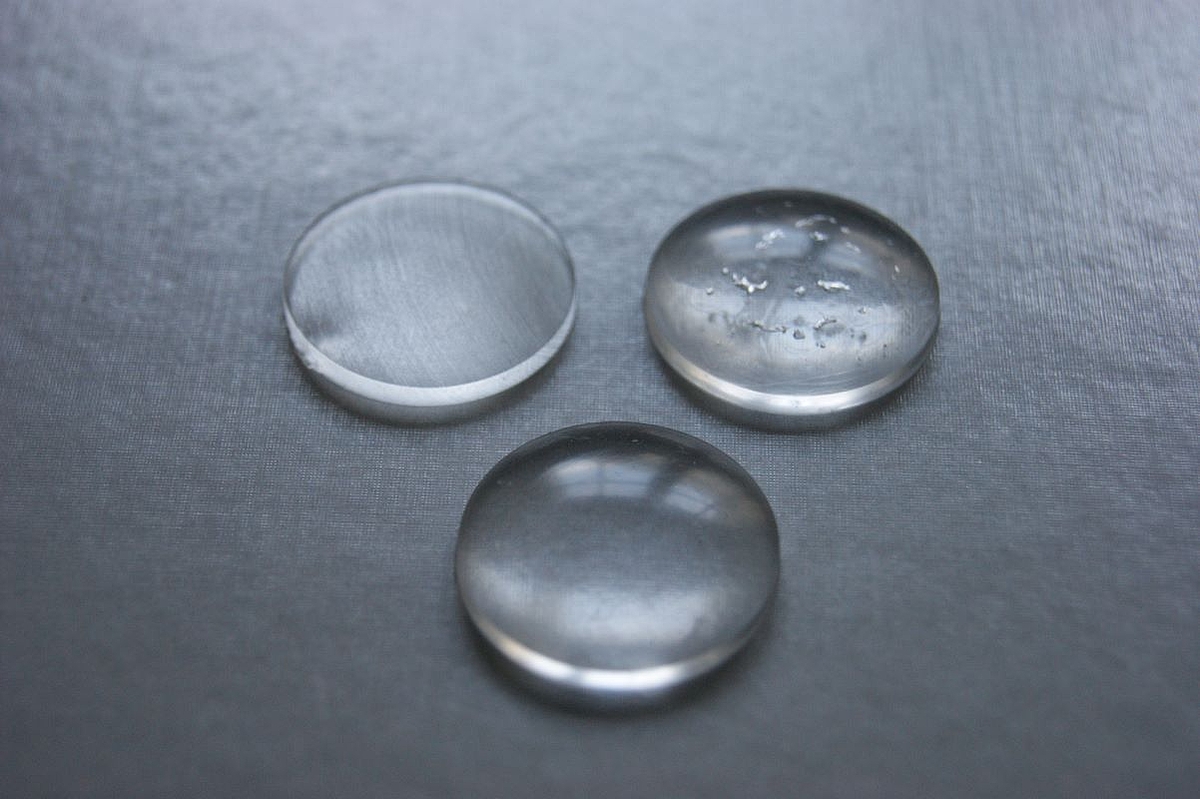
Noch kleinere Strukturen im Nano-Bereich lassen sich durch die Zwei-Photonen-Polymerisation (2PP) in photoaktiven Polymeren erzeugen. Dieses Verfahren wurde in den letzten Jahren zunehmend erforscht und genügt den hohen Ansprüchen an Präzision und Homogenität im Bereich der Photonik.
Die kommerzielle 2PP-Technologie basiert jedoch auf Femtosekunden-Lasern, welche kostenintensiv in der Anschaffung, zeitintensiv in der Wartung und sensitiv gegenüber Umwelteinflüssen sind. Um industrietaugliche 2PP-Systeme für den 3D-Druck von Polymeren zu entwickeln, werden in der Task Group M2 gütegeschaltete Mikrochip-Laser erforscht und in 2PP-Fertigungsanlagen integriert. Letztere zeichnen sich durch eine hohe Effizienz, eine kompakte Bauform und geringe Kosten aus und erreichen Präzision und Materialdurchsatz in der Größenordnung von konventionellen Femtosekunden-Lasern [10].
Durch die zielgerichtete Kombination der Technologien werden sowohl funktional als auch fertigungstechnisch auf Komponenten- und Systemebene völlig neue Lösungen entstehen die wir in den nächsten Jahren anhand von Demonstratoren verifizieren werden.
Prof. Dr. Ing. Roland Lachmayer ist seit 2011 Gründungsdirektor des Instituts für Produktentwicklung und Gerätebau der LUH. Er ist wissenschaftlicher Beirat des Laser Zentrum Hannover e.V., Geschäftsführer der WiGeP (Wissenschaftlichen Gesellschaft für Produktentwicklung e.V.), Senator der LUH und ist neben einigen hundert Veröffentlichungen Mitherausgeber von sechs Büchern/Tagungsbänden zur Additiven Fertigung.
Dr. Moritz Hinkelmann leitet seit 2020 die Gruppe Optische Systeme in der Abteilung Laserentwicklung am Laser Zentrum Hannover e.V. Seine Hauptforschungsgebiete umfassen die Simulation und generative Fertigung funktionaler Optiken sowie das Design und die Konstruktion optischer Systeme.
Ausgewählte Literatur:
[1] R. Lachmayer, B. Lippert: Entwicklungsmethodik für die Additive Fertigung, Springer Nature, Berlin, 2020, ISBN 978-3-662-59788-0
[2] Biermann, T.; Ley, P.-P.; Ziebehl, A.; Feldmann, J.; Lachmayer, R.; Konzepte für die Additive Fertigung optischer Elemente mit hochtransparenten Silikonwerkstoffen; Konstruktion für die additive Fertigung, Springer Vieweg, 2021
[3] Biermann, T.; Grabe, T.; Ley, P.-P; Hüchting, J.; Lachmayer, R.; Potentials and challenges of additive manufacturing using highly transparent silicone materials; DGaO-Proceedings, ISSN: 1614-8436, 2020
[4] P. Von Witzendorff, L. Pohl, O. Suttmann, P. Heinrich, A. Heinrich, J. Zander, H. Bragard, and S. Kaierle, „Additive manufacturing of glass: CO2-Laser glass deposition printing,“ Conference on Photonic Technologies (2018).
[5] K. Rettschlag, F. Kranert, A. Hohnholz, A. Wienke, O. Suttmann, J. Neumann, D. Kracht, and R. Lachmayer, „Laser deposition of fused silica coreless fibers to generate functional waveguides, “ Laser in Manufacturing Conference (2019).
[6] F. Kranert, K. Rettschlag, A. Wienke, A. Hohnholz, J. Neumann, P. Jäschke, D. Kracht, and R. Lachmayer, „Generation of functional curved waveguides by CO2-laser based deposition of coreless fused silica fibers,” Proc. SPIE 11349 (2020). DOI: https://doi.org/10.1117/12.2554516
[7] T. J. Hinton, Q. Jallerat, R. N. Palchesko, J. H. Park, M. S. Grodzicki, H.-J. Shue, M. H. Ramadan, A. R. Hudson, and A. W. Feinberg, “Three-dimensional printing of complex biological structures by freeform reversible embedding of suspended hydrogels,” Sci. Adv. 1(9), 1-10 (2015). DOI: 10.1126/sciadv.1500758
[8] T. Wolfer, P. Bollgruen, D. Mager, L. Overmeyer, and J. G. Korvink, „Printing and preparation of integrated optical waveguides for optronic sensor networks,” Mechatronics 34, 119-127 (2016). DOI: 10.1016/j.mechatronics.2015.05.004
[9] D. Perevoznik and U. Morgner, „Femtosecond writing of waveguides and waveguide network components,” CLEO-Europe/EQEC 2019.
[10] D. Perevoznik, R. Nazhir, R. Kiyan, K. Kurselis, B. Koszarna, D. T. Gryko, and B. N. Chichkov, „High-speed two-photon polymerization 3D printing with a microchip laser at its fundamental wavelength,” Optics Express 27(18), 25119-25125 (2019). https://doi.org/10.1364/OE.27.025119
Ansprechpartner


30823 Garbsen


30823 Garbsen