Meet us personally or follow our news channels.
Our Motivation
Optical technologies are key technologies of the 21st century. In the form of smartphone displays or fast fibre-optic Internet, for example, they have provided a giant technological leap forward. However, conventional optical systems such as projectors, microscopes or lasers still consist of a large number of discrete optical components which generate, manipulate or detect the light used.
While micro integration in the field of electronics towards electronic semiconductor chips has been standard for decades, PhoenixD has set itself the goal of transferring the success in microelectronics to optical technologies. To this end, new types of process technologies are being researched and further developed, which enable the inexpensive and precise development and production of integrated photonic assemblies.
In this context, additive manufacturing is one of the enablers to achieve the goal of integrated photonics. Where conventional manufacturing processes reach their limits, generative manufacturing shows its strengths: short development times, integrated and optimised effects, innovative design possibilities as well as a significant reduction of the required resources and optimised process chains.
By combining different material groups such as polymers, ceramics and glass in a generative process chain, tailor-made material properties and very high functional integration can be achieved. They are a prerequisite for automated manufacturing and economical solutions in the product life cycle.
In this way, optical products that are still very difficult and expensive to manufacture today, for example in medical technology, traffic engineering or process technology, can be realised more efficiently and made available for a much more comprehensive range of applications. "We imagine, for example, making medical analysis in pocket format affordable for everyone," says Dr. Moritz Hinkelmann, who has headed the Optical Systems Group in the Laser Development Department at the Laser Zentrum Hannover e.V. since 2020. His main research areas include the simulation and generative manufacturing of functional optics as well as the design and construction of optical systems.
Our Research
Due to their quality, additive-manufactured optics have come to use so far only in a few areas. These components have to fulfil high demands in terms of optical quality and the properties of the element. Consequently, the manufactured piece must have, among other things, a defined refractive index and transmission (transmittance), a low coefficient of thermal expansion and sufficient homogeneity. A further challenge is to integrate the production of optical elements with low surface roughness and material combinations into one process.
In the field of additive manufacturing of optical components and systems, various laser-based processes have become established which address different size scales and precision [1]. In particular, transparent polymers, silicone [2,3] and quartz glass are used to produce functional optics. Task Group M2 investigates these approaches to the production of transparent optics in several subprojects concerning process optimisation, simulation and quality of the optical properties.
In the field of optical systems with discrete components, quartz glass is used today, which is often processed manually in complex processes. The additive manufacturing of quartz glass opens up new possibilities concerning design and thus applications.
However, 3D printing of glass is an almost unexplored field, which is further developed in a so-called Laser Glass Deposition process [4]. Here, a glass filament is applied to a glass substrate utilising Carbon Dioxide Laser radiation (Figure 1).
In addition to classic optical fibres [5,6], these printers can also produce structural elements such as low-weight stiffeners for scanner mirrors. The corresponding selection of suitable process parameters is carried out with the aid of a new simulation model which simulates the manufacturing process and thus the temperature distribution which is essential for the selection of a suitable process window.



In another project, a team of scientists investigate the potential of highly transparent silicone materials. These materials benefit from their high resistance to UV radiation, temperature and environmental influences as well as from high material flexibility and low density. Researchers examine various silicones for their suitability for optical applications (see Figure 2). Based on the material requirements, they develop methodically fitting manufacturing processes and implement these subsequently.
Freeform-Reversible-Embedding [7] technologies are used here, in which a material combination is selectively introduced into a non-reactive liquid and cured by UV radiation. In the future, researchers will produce temperature-resistant, silicone-based free-form optics generatively at low cost and with low surface roughness. Scientists will develop further alternatives to manipulate their geometry and thus, their optical properties using actuators based on the flexibility of silicone.
In addition to the processes mentioned above, in which the material is fed locally into the process zone, entire optical networks can be printed cost-effectively in a short time using glass wafers or roll-to-roll processes. This approach, called Flexographic Printing, enables the individualised mass production of planar sensor networks [8]. It can be used, for example, for highly integrated data networks and, in combination with elements manufactured in a batch process, should also be used for medium performance applications.
One possibility for writing buried, single-mode waveguides is so-called femtosecond direct writing [9]. Here, femtosecond lasers structure targeted polymers in volume. With the high intensities of the laser beam, a plasma is generated, which induces local material stresses and thus a change in the refractive index.
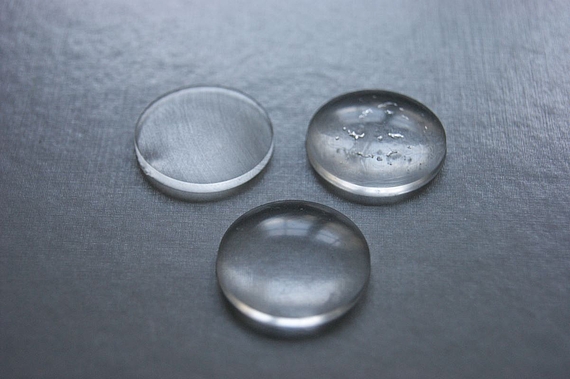
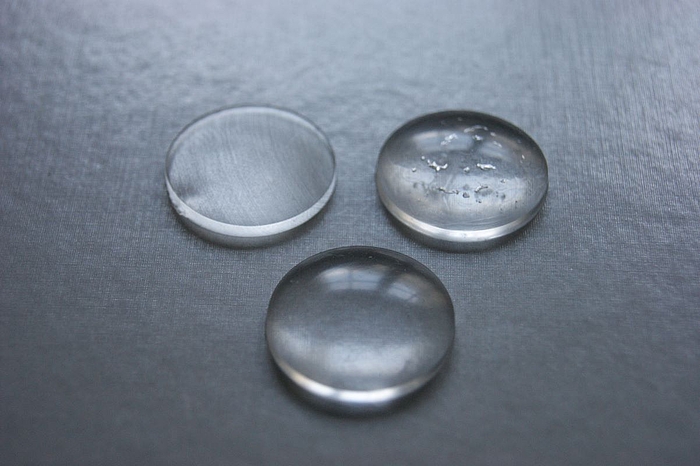
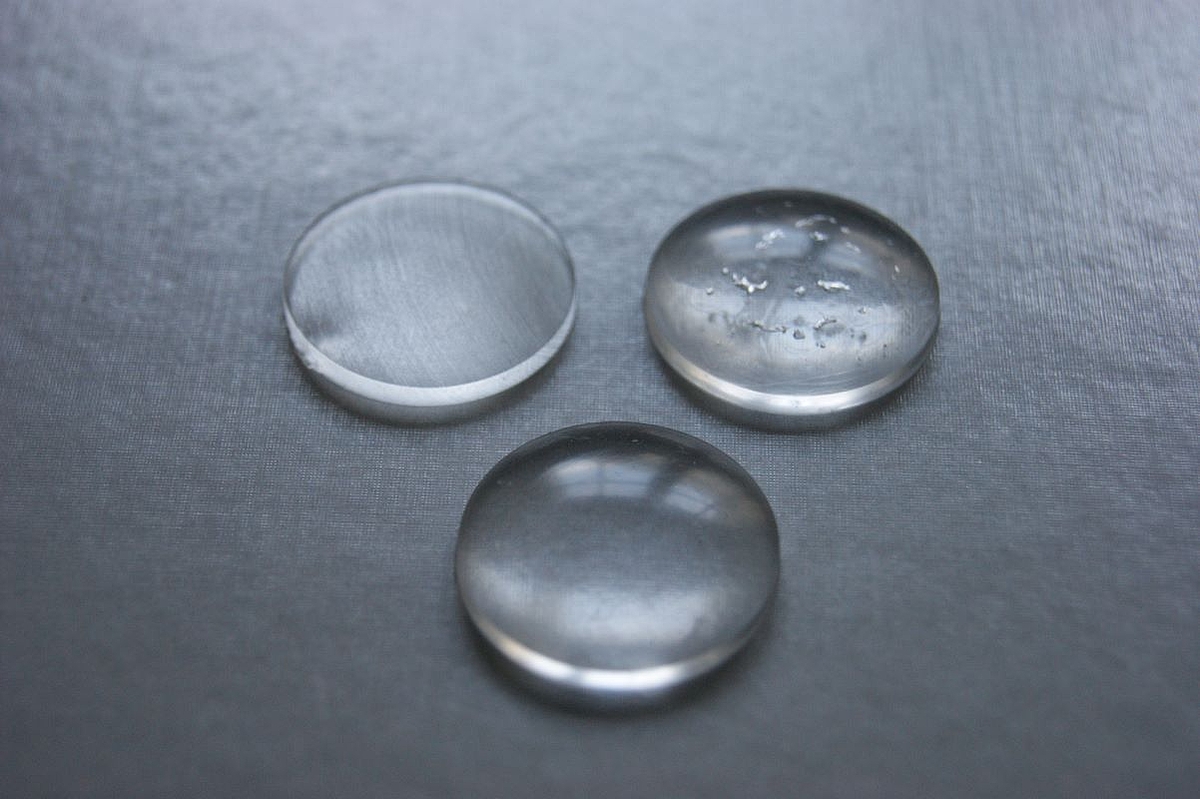
Even smaller structures in the nano range can be created by two-photon polymerisation (2PP) in photoactive polymers. This process has been increasingly researched in recent years and meets the high demands for precision and homogeneity in the field of photonics.
However, commercial 2PP technology relies on femtosecond lasers, which are cost-intensive to purchase, time-consuming to maintain and sensitive to environmental influences. To develop industrial 2PP systems for the 3D printing of polymers, the Task Group M2 is researching Q-switched microchip lasers and integrate them into 2PP production facilities. The latter is characterised by high efficiency, compact design and low costs and achieve precision and material throughput on the scale of conventional femtosecond lasers [10].
The targeted combination of the technologies will lead to entirely new solutions both functionally and in terms of production technology at component and system level, which we will verify in the next few years using demonstrators.
Prof. Dr. Ing. Roland Lachmayer has been founding director of the Institute for Product Development and Equipment Construction at LUH since 2011. He is a scientific advisor to the Laser Zentrum Hannover e.V., managing director of WiGeP (Wissenschaftliche Gesellschaft für Produktentwicklung e.V.), a senator at LUH and, in addition to several hundred publications, is co-editor of six books/conference proceedings on additive manufacturing.
Dr. Moritz Hinkelmann has been head of the Optical Systems Group in the Laser Development Department at the Laser Zentrum Hannover e.V. since 2020. His main research areas include the simulation and generative manufacturing of functional optics as well as the design and construction of optical systems.
Selected Publications:
[1] R. Lachmayer, B. Lippert: Entwicklungsmethodik für die Additive Fertigung, Springer Nature, Berlin, 2020, ISBN 978-3-662-59788-0
[2] Biermann, T.; Ley, P.-P.; Ziebehl, A.; Feldmann, J.; Lachmayer, R.; Konzepte für die Additive Fertigung optischer Elemente mit hochtransparenten Silikonwerkstoffen; Konstruktion für die additive Fertigung, Springer Vieweg, 2021
[3] Biermann, T.; Grabe, T.; Ley, P.-P; Hüchting, J.; Lachmayer, R.; Potentials and challenges of additive manufacturing using highly transparent silicone materials; DGaO-Proceedings, ISSN: 1614-8436, 2020
[4] P. Von Witzendorff, L. Pohl, O. Suttmann, P. Heinrich, A. Heinrich, J. Zander, H. Bragard, and S. Kaierle, „Additive manufacturing of glass: CO2-Laser glass deposition printing,“ Conference on Photonic Technologies (2018).
[5] K. Rettschlag, F. Kranert, A. Hohnholz, A. Wienke, O. Suttmann, J. Neumann, D. Kracht, and R. Lachmayer, „Laser deposition of fused silica coreless fibers to generate functional waveguides, “ Laser in Manufacturing Conference (2019).
[6] F. Kranert, K. Rettschlag, A. Wienke, A. Hohnholz, J. Neumann, P. Jäschke, D. Kracht, and R. Lachmayer, „Generation of functional curved waveguides by CO2-laser based deposition of coreless fused silica fibers,” Proc. SPIE 11349 (2020). DOI: https://doi.org/10.1117/12.2554516
[7] T. J. Hinton, Q. Jallerat, R. N. Palchesko, J. H. Park, M. S. Grodzicki, H.-J. Shue, M. H. Ramadan, A. R. Hudson, and A. W. Feinberg, “Three-dimensional printing of complex biological structures by freeform reversible embedding of suspended hydrogels,” Sci. Adv. 1(9), 1-10 (2015). DOI: 10.1126/sciadv.1500758
[8] T. Wolfer, P. Bollgruen, D. Mager, L. Overmeyer, and J. G. Korvink, „Printing and preparation of integrated optical waveguides for optronic sensor networks,” Mechatronics 34, 119-127 (2016). DOI: 10.1016/j.mechatronics.2015.05.004
[9] D. Perevoznik and U. Morgner, „Femtosecond writing of waveguides and waveguide network components,” CLEO-Europe/EQEC 2019.
[10] D. Perevoznik, R. Nazhir, R. Kiyan, K. Kurselis, B. Koszarna, D. T. Gryko, and B. N. Chichkov, „High-speed two-photon polymerization 3D printing with a microchip laser at its fundamental wavelength,” Optics Express 27(18), 25119-25125 (2019). https://doi.org/10.1364/OE.27.025119
Contact


30823 Garbsen


30823 Garbsen