Treffen Sie uns persönlich oder verfolgen Sie unsere News-Kanäle.
Diese sollen zudem soweit wie möglich direkt in die Produktionsprozesse integriert werden, um sowohl eine hochgenaue Charakterisierung der Bauteile als auch eine Steuerung und Optimierung der Produktion zu gewährleisten. Die Präzisionsmetrologie aus der Arbeitsgruppe F1 wird dabei mit den in der Arbeitsgruppe F2 entwickelten Konzepten zur adaptiven Steuerung der Produktion und der Realisierung eines virtuellen Bauteilmodells („digitaler Zwilling“) auf Basis von Ansätzen der künstlichen Intelligenz (KI) verbunden, um eine automatisierte, sich selbst optimierende Fertigungskette zu entwickeln.
Die in Arbeitsgruppe F1 generierten umfassenden Messdaten dienen auch als Input für die in PhoenixD entwickelten multiskaligen Simulationen sowohl der Bauteil-Funktionalität als auch der Fertigungsprozesse selbst, wodurch ein tieferes Verständnis der zugrunde liegenden physikalischen Effekte und Abhängigkeiten während der Herstellung erreicht wird und neuartige optische Systeme für Anwendungen entstehen.
Beispiele für solche Anwendungen liegen wir unter anderem in der Detektion von Biomolekülen, der Point-of-Care Diagnostik, dem Umweltmonitoring und der medizinischen Bildgebung und Analytik.
Wie fügt sich dieser Aspekt in die übergeordnete Strategie von PhoenixD ein, neuartige optische Technologien zu entwickeln und zu bauen?
In der Arbeitsgruppe F1 werden sowohl neue, echtzeitfähige Inline-Messtechniken zur Integration in die Fertigungsprozesse als auch hochpräzise Offline-Metrologie für die genaue Charakterisierung der gefertigten optischen Bauteile und Systeme entwickelt.
Diese sind einerseits für die Realisierung adaptiver Fertigungsketten notwendig und sollen andererseits wichtige Erkenntnisse zur Funktionalität der optischen Systeme, zur Material- und Prozessentwicklung sowie zur multiskaligen Simulation liefern.
Ultimativ wird dadurch (i) eine integrierte und ressourcen- wie kosteneffiziente Fertigung präzisionsoptischer Bauteile und Systeme in einer vollständig vernetzen und automatisierten Produktionsumgebung, speziell auch für kleine Losgrößen, (ii) eine umfassende multiphysikalische Beschreibung aller relevanten Effekte und (iii) eine Validierung der funktionalen Systeme für neue Anwendungen ermöglicht.
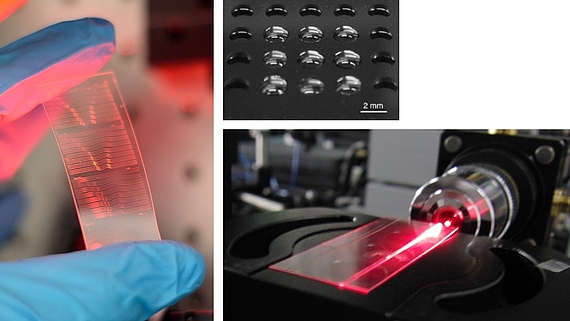
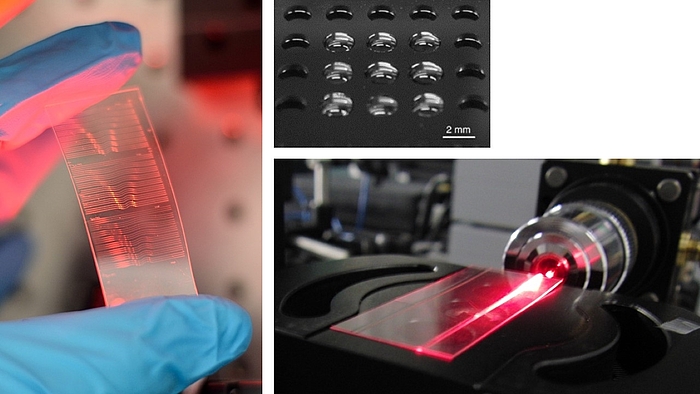

Mit welchen anderen Arbeitsgruppen arbeiten Sie dafür besonders eng zusammen?
Die Aktivitäten der Arbeitsgruppe F1 sind eng zum Beispiel mit der Entwicklung der Konzepte zur adaptiven Produktion und Realisierung der virtuellen Bauteilmodelle (Arbeitsgruppe F2), der Materialentwicklung, additiven Fertigung und Integration (Arbeitsgruppen M1, M2, M3 und M6) sowie der Simulation der optischen Materialien (Arbeitsgruppe S2) und der linearen und nichtlinearen Systemfunktionalitäten (Arbeitsgruppe S3) verwoben.
Die möglichst umfassende multiphysikalische Beschreibung optischer Funktionen und Prozesse erfordert die Verifizierung der Simulationen durch experimentelle Daten, um effiziente und dennoch physikalisch korrekte Modelle für die eingesetzten Materialien und erforschten individuellen Optiken zu entwickeln (Arbeitsgruppen S2 und S3).
Bei der Produktion zielt PhoenixD auf vernetzte Prozesse ab, so dass komplexe optische Systeme durchgängig in einer Prozesskette realisiert werden können. Hier ist eine enge Abstimmung mit allen Batch- und kontinuierlichen Fertigungstechnologien erforderlich (zum Beispiel mit den Arbeitsgruppen M2 und M3).
Für die Funktionalisierung der optischen Bauteile ist die Verbindung zu den Datenwissenschaften und der Informationstechnik essenziell, die geeignete optoelektronische Schnittstellen entwickeln. Auf diese Weise werden die für jedes System individuellen virtuellen Modelle erstellt sowie die KI-Algorithmen implementiert, um zukünftige Produktion basierend auf Echtzeit-Messdaten zu verbessern.
Welche Anwendungszwecke könnten Sie sich nach derzeitigem Stand künftig vorstellen?
Wesentliche Anwendungen liegen in der Multiplex-Detektion von Biomolekülen in den Lebenswissenschaften und der Medizin, dem Monitoring von Toxinen in der Umwelt, der Überwachung von Lebensmittelherstellung und Produktionsprozessen in der Industrie, der medizinischen Point-of-Care Diagnostik sowie der optischen Kontrolle und Steuerung von Pflanzenwachstum beim Digital Farming.
Individualisierte, adaptive und lernende Systeme, die mittels Methoden der additiven Fertigung realisiert werden, können dabei neue Anwendungsfelder erschließen oder bestehenden Bedarfe in Wissenschaft, Wirtschaft und Industrie decken.
Was uns antreibt
Funktionale optische Systeme können nützliche Alternativen zu den elektronisch-basierten Lösungen bieten. Jedoch ist deren Herstellung derzeit noch recht komplex und daher in vielen Fällen weder kosten- noch ressourceneffizient.
Die Entwicklung von modernen, additiven Fertigungsmethoden in Kombination mit Algorithmen der künstlichen Intelligenz zur Verarbeitung großer Datenmengen, die ihr großes Potenzial im Zuge von globalen Trends wie Industrie 4.0 oder Internet of Things (dt. Internet der Dinge) bereits angedeutet haben, können zu einer Revolution in der Optikfertigung der Zukunft führen. Voraussetzung dafür ist, dass mittels solcher Fertigungsmethoden individuelle Elemente und sogar ganze funktionale Systeme mit optischer Qualität bereits integriert realisiert werden können.
Unsere Aktivitäten fokussieren sich auf die Erforschung der Fertigung mikro- und nanooptischer Komponenten auf Polymerbasis und deren Anwendung für sensorische und messtechnische Aufgaben. Um diese Ziel zu erreichen, entwickeln wir hochpräzise und echtzeitfähige Messtechnik, die notwendig ist, um Ungenauigkeiten bei der Produktion bereits im Prozess zu erkennen und in Verbindung mit einer ebenso echtzeitfähigen Funktionssimulation zu korrigieren.
Insbesondere setzen wir bei der Fertigung optischer Elemente auch neuartige Materialien ein, die zum einen neue System-Funktionen erlauben und zum anderen den Nachhaltigkeitsaspekt bei der Fertigung berücksichtigen. Letztlich sollen dadurch der Ressourcenverbrauch und der ökologische Fußabdruck der neuen Bauteile und Systeme minimiert und die Kosten so weit reduziert werden, dass sie zukünftig breiten und derzeit zum Teil nicht möglichen Anwendungsfeldern in allen Gesellschaftsschichten zur Verfügung stehen.
Unsere Forschungsarbeit
Wir wenden Methoden der additiven und subtraktiven Fertigung wie etwa Laser-Direkt-Schreiben, Fotolithographie oder Imprint-Replikation an, um sensorisch-optische Funktionalität auf Polymerbasis zu realisieren. Als Materialklassen werden fotosensitive Polymere eingesetzt.
Die für eine messtechnische Aufgabenstellung notwendigen Systeme werden mittels mikro- und nanooptischer Elemente realisiert und durch 2D- und 3D-Integration zu vollständigen Funktionseinheiten zusammengesetzt. Neben der präzisen Fertigung auf Basis eines optimierten Designmodells ist die Echtzeit-Überwachung und -adaption der Produktion und die umfassende Charakterisierung der Bauteile für deren Funktionalität entscheidend.
Die Entwicklung einer sich selbst optimierenden Fertigungskette erfordert deren Umsetzung in einem geschlossenen Kreislauf (Feedback-Loop), der Simulation und Herstellung kontinuierlich mittels der Präzisionsmetrologie rückkoppelt und anpasst, so dass Fehler in der Produktion noch während des Prozesses erkannt und kompensiert werden können.
Die Funktionalität der gefertigten Bauteile wird durch präzise Offline-Messtechnik z.B. auf Basis von Interferometrie sowie optischer und Atom-Kraftmikroskopie charakterisiert. Daraus werden Erkenntnisse über das Verhalten der Materialien Strukturen sowie der Messfunktion abgeleitet.



Inline-Metrologie z.B. basierend auf Nahfeld-Messkonzepten oder spektroskopischer Ellipsometrie wird in die Prozessketten integriert, um die Qualität hergestellter Strukturen zu überprüfen und gegebenenfalls zu korrigieren. Auch kohärente Röntgenmesstechnik wird langfristig eingesetzt, um Messungen unabhängig von Materialparametern zu ermöglichen.



Um diese Vision zu realisieren, ist die Zusammenarbeit mit vielen Arbeitsgruppen des Exzellenzclusters PhoenixD erforderlich. Beispielsweise werden im Cluster neue Materialien entwickelt, mit denen passive und aktive Elemente realisiert werden können. Auch die Entwicklung von Herstellungsmethoden für hybride Materialien und deren Modellierung und Simulation ist für unsere Forschung relevant.



Zudem arbeiten wir eng mit den Arbeitsgruppen zusammen, die sich mit der 2D- und 3D-Integration, der funktionellen Beschichtung und der elektronischen Ansteuerung der Systeme beschäftigen (Arbeitsgruppen M5 und M6).
Schließlich werden die im Prozess erhobenen Maschinen- und Charakterisierungsdaten mittels geeigneter Schnittstellen zusammengeführt, um eine sich ständig optimierende Produktionsumgebung in einer geschlossenen Rückkopplungsschleife, dem Feedback-Loop zu schaffen (Arbeitsgruppe F2). Dazu kooperieren wir mit der Arbeitsgruppe S4, die geeignete Schnittstellen und Übergabepunkt entwickelt.
Ansprechpartner


30167 Hannover

